Conco technology considerably improves quality and saves time on cleaning at Argentine Thermal Power Plant followed by Eddy Current Test.
PLANT: Central Térmica Vuelta de Obligado
COUNTRY: Argentina
CLEANING DATE: May 11 to May 13, 2019
NUMBER OF TUBES: 6,800
TUBE MATERIAL: Stainless Steel SA-249Tp-316-L
TYPE OF CLEANING: Mechanical
EQUIPMENT USED: ProSeries Pump
CLEANERS USED: H-Brush (1”x22 and 1”x20)
DEPOSIT TYPE: Clay
Introduction:
The electricity sector in Argentina is the third largest electricity market in Latin America, behind Brazil and Mexico, and is the 31st in the world. The matrix of Argentina depends primarily on fossil fueled power plantas (approximately 63% in 2019). For this reason, it is important to be able to provide Conco services mainly in the thermal power plants of our country. These plants are the ones with the largest equipment and also have the resources to perform the services.
One of the most important plants is CVO (Central Térmica Vuelta de Obligado), who on this occasion asked us to clean and subsequently inspect a condenser with the following specificacitons:
DENOMINATION TYPE: Condensador Foster Wheeler / GE Energy
TYPE: Surface Condenser
NUMBER OF TUBES: 26.946 (2426 Impingement y 24.520 main)rgentina
TYPE OF TUBES: Straight
LENGTH OF TUBES: 39" (11.648 mm)
EXTERNAL DIAMETER: 1"
INTERNAL DIAMETER: 0.944" main / 0.930" Impingement
TUBES MATERIAL: Stainless Steel SA-249Tp-316-L
WATER BOXES: 6 totales (4 entry and exit 2 returns)
Problem:
The main problem that CVO had was knowing if the condenser was in good condition after 3 years of operation (because the equipment is under manufacturer “warranty”). This equipment was assembled in 2016 and CVO made an Eddy Current Test with Conco – Kinetic to determine the initial state and have references as starting point. At this time, in 2019, the client decided that the equipment should be opened, cleaned and performed a new Eddy Current Test to the same tubes.
They wanted a comparison of results to know if the operation is correct.
To achieve a correct inspection, Kinetic proposed to the client the Conco ProSeries cleaning. On this occasion the cleaners used for the type of dirt present were the H-Brsuh. Mainly cleaners 1”x22 were used but also some of 1”x20 (because there are two measures of tubes in the equipment).
Solution:
For this, suitable Kinetic Staff were used, who based on the equipment drawings could mark wich were the tubes inspected in 2016. The tubes were cleaned using Conco ProSeries H-Brush cleaners.
In the first image, we can see the cleaners placed in the condenser to be passed.
In the Picture 2, the Kinetic staff is working on cleaning the equipment. For this, pumps, hoses and Conco water guns were used.
This procedure was very careful and the staff made sure that all the cleaners had passed by counting them.
Once that the internal tubes cleaning was completed, the Kinetic Staff completely cleaned the work area and dried the tubes (Picture 3).
Results:
The cleaning results were excellents. This could be determined by the following:
- The clients were very satisfied. On the one hand, General Electric, who requested the cleaning, and on the other, CVO, who requested the Eddy Current Test. All tubes could be inspected without any problems to pass the probe.
- If a comparison is made of Conco cleaning times with high pressure water, wich in this case took 3 days, it would have taken approximately 12 days.
Picture 4, shows the cleaners at the outlet of the tubes and in Picture 5 the tubes after cleaning with Conco ProSeries.
In conclusion, there is evidence that in the thermal power plants prior to the realization of an Eddy Current Test, it is always convenient to use Conco ProSeries Technology.

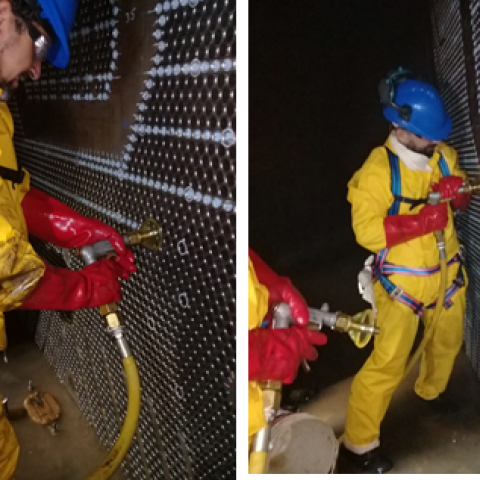
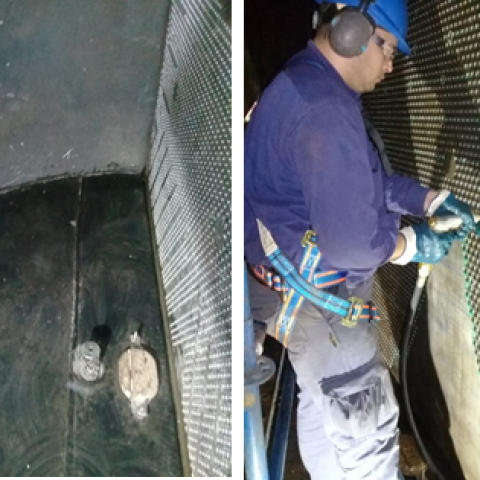
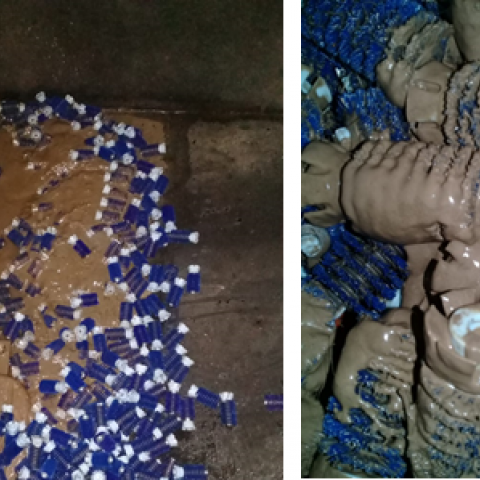
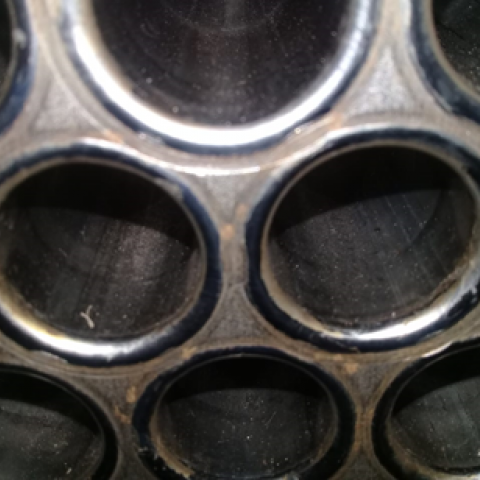